Fosroc Galvashield® Anodes are a cuttingedge solution designed to combat corrosion in concrete structures. Corrosion poses a significant threat to the durability and longevity of reinforced concrete, particularly in harsh environments or when exposed to aggressive elements.
|
|
Fosroc Galvashield® Anodes employ advanced galvanic technology to provide localized cathodic protection, preventing the onset and progression of corrosion. These anodes act sacrificially, effectively diverting corrosive currents away from vulnerable areas and preserving the structural integrity of the concrete.
|
|
|
|
|
Available in a range of configurations, Fosroc Galvashield® anodes can be easily installed on both new and existing structures. They are specifically designed to target critical areas, such as rebars, steel connectors, and embedded metal components, providing targeted protection where it is needed the most. Once installed, they operate autonomously, ensuring continuous protection for an extended period. This not only helps to reduce maintenance costs but also minimizes disruptions to ongoing operations.
Fosroc Galvashield® anodes have been extensively tested and proven to deliver excellent results in various applications, including bridges, marine structures, parking garages, and industrial facilities. They provide an effective, long-term solution to mitigate corrosion-related issues, prolonging the service life of concrete structures and
|
|
minimizing the need for costly repairs or replacements. With Fosroc Galvashield® anodes, clients can have peace of mind knowing that their concrete structures are protected against the detrimental effects of corrosion, ensuring enhanced durability, safety, and cost-effectiveness.
|
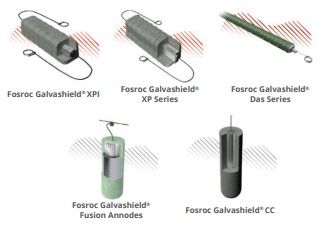 |
|
|
|
Galvashield® anodes as a whole have following key features and benefits
•Proven technology: Fosroc Galvashield® is the original embedded galvanic anode with over a 20-year track record.
•Long lasting: minimum 20 year anode service life when using standard design tables; reduces the need for future repairs.
• Independent testing: indicates concrete repair service life can be extended by more than 400%.
• Type 1A or 2A anodes: alkali-activated to maintain activity of zinc; meets building code requirements that prohibit intentionally added constituents that are corrosive to reinforcement within repair area.
• One-and-Done™: connection innovative single wire connection can be installed up to 2x faster than the traditional two wire connection, saving 50% on installation labour cost (for XP and XPI series).
|
|
• Cast zinc core: provides high anode utilization and a secure long-term connection between the zinc and the integral lead wire.
|
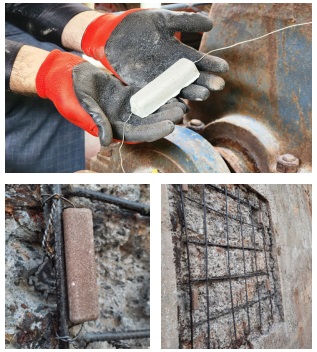 |
|
|
|
|
• BarFit™ design: grooved edges on Fosroc Galvashield® XP2, XP4 and XPX anodes assist with secure anode placement.
• Integral steel connection wires: provides dependable steel-to-steel contact with no intermediate materials such as galvanizing that may compromise the long-term electrical connection.
• Economical: provides localized protection where it is needed the most, at the interface between the repair and the remaining contaminated concrete.
|
|
• Versatile: can be used for both conventionally reinforced and prestressed or post-tensioned concrete.
• Low maintenance: requires no external power source or system monitoring.
• ICRI CSP-3 (Concrete Surface Profile): raised ridges provide increased surface profile to promote mechanical bond with repair mortars and concrete.
|
|
|
|
|
1. Checking steel connectivity of existing rebars at site (< 1mV) establish connection if required
|
|
|
2. Clean the rebar with Reebaklens RR one day prior and with sandpaper to establish fresh steel surface for new connection establishment
|
|
3. All Steel connections completed and reading on the multimeter as 0.00 mV
|
|
|
|
4. Tie the anodes at designed spacing on reinforcement ensuring cover
|
|
|
5. Perform a final Potential difference check from steel to steel, anode to steel and anode to anode
|
|
6. Using polymer modified mortar or micro concrete to repair the area
|
|
|
|
Do’s
Pre-Wet the anodes so that cement slurry does not block the pores.
Establishing electrical continuity of reinforcing steel at site.
Take care while looping wires, no gap
should be left between reinforcement and anode tie wire.
Check continuity of steel to steel, anode to steel and anode to anode.
Always provide adequate cover to anodes.
Engulf the anodes with low resistivity mortar/concrete/Micro-concrete.
|
|
Don’t
Don’t overtwist the anode tie wires.
Do not apply bond coat on anode surface / tie wires.
Don’t use bonding agent in sphere of influence of anodes during patch repairs.
Don’t immerse the anodes in water for longer periods.
Don’t break the encapsulating mortar.
Don’t tie anodes to corroded steel.
Don’t apply protective coating where the anodes are tied to reinforcing steel and neither over anodes or tie wires.
|
|
|
|
|
|
Fosroc Chemicals (India) Private Limited
Embassy Point, No.150, 2nd Floor, Infantry Road,
Bangalore - 560001
Tel.: +91 80 4252 1900 • Fax: +91 80 2228 1510
Email: enquiry.india@fosroc.com
Website: www.fosroc.com
|
|
For product info and solutions assistance.
|
CONTACT US |
|
|
|
|
|
|
|
|